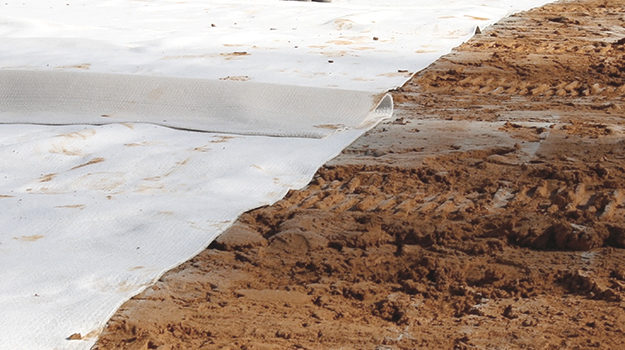
There is almost certainly at least one nonwoven fabric in the vicinity of where you are sitting or standing right now. Maybe a tea bag or a coffee filter? A filter for air conditioning. Diapers, bleach wipes, and lens tissues are definitely a face mask or seven.
Though the COVID-19 outbreak undoubtedly raised awareness of nonwoven materials. We’ve been keeping an eye on this expanding market segment for years. Why? Because the pressure-sensitive adhesive tape is frequently utilized in the fabrication or conversion of these textiles into useful everyday products.
Here’s our opinion on how non-woven will evolve and play an important part in the convenience economy.
What is non-woven?
Nonwoven fabrics are the most basic and oldest types of textile fabrics. Non-woven fabrics, as the name implies, are sheet or web structures that are mechanically, thermally, or chemically bound together by entangling fiber or filaments.
They are porous flat or tufted sheets manufactured from individual fibers, molten plastic, or plastic film. They are not manufactured by weaving or knitting and do not require the fibers to be converted to yarn.
Non-woven fabrics typically contain a particular percentage of recycled fabrics and oil-based materials. The percentage of recycled fabrics varies according to the strength of the material required for the specific use. Furthermore, with the correct treatment and facilities, some nonwoven textiles can be recycled after use. As a result, some perceive non-woven fabrics to be more environmentally friendly for specific applications, particularly in fields and businesses where disposable or single-use products are vital, such as hospitals, schools, nursing homes, and luxury hotels.
How are nonwoven fabrics manufactured?
Non-woven fabrics are produced using one of two methods: felted or bonded. Felted non-woven fabric is made by layering thin sheets and then compressing the fibers with heat, moisture, and pressure to create a thick matted material that will not travel or fray.
The following are the primary ways for producing bonded non-woven fabrics: Dry Laid, Wet Laid, and Direct Spun are the three types of yarn.
In the production of Dry Laid Non-woven Fabric, a web of fibers is laid in a drum and hot air is pumped to fuse the fibers together.
- Wet-Laid involves mixing a web of fibers with a softening solvent, which produces a glue-like substance that links the fibers together, and then lays the web out to dry.
- In Direct Spun, the fibers are spun onto a conveyor belt and sprayed with adhesive before being pushed to join. (Glue is not necessary for thermoplastic fibers.)
How are non-woven fabrics being used?
Nonwoven fabrics are used in a variety of industries, including medical, fashion, automotive, filtration, construction, geotextiles, and protective materials. The use of non-woven fabrics is rising day by day, and our current way of life would be unintelligible without them. Nonwovens, in fact, play an important role in the convenience economy.
Nonwoven fabric is classified into two types: durable and disposable. Nonwoven cloth is approximately 60% durable and 40% disposable. These specialty fabrics are designed to perform certain purposes like absorbency, sterility, liquid repellency, resilience, stretch, softness, strength, flame retardancy, cushioning, thermal insulation, acoustic insulation, and filtration. These characteristics are frequently combined to make fabrics that are suitable for certain purposes. While maintaining a good balance between product use-life and cost.
Industries where the non-woven fabric was used
Non-woven fabrics are most commonly utilized in the following industries:
- Health and hygiene. Diapers, feminine hygiene products, adult incontinence products, wipes (personal care and fingernail care), cosmetic facial pads, and consumer face masks
- Geotextiles and Buildings. Erosion control, canal construction, drainage systems, geo-membrane protection, sand infiltration barrier for drainage tile, landfill liners, insulation (fiberglass batting), weather-resistant house wrap, plant potting materials, in some cases best clay liner by Clay Liner suppliers also used for it.
- Industrial. Carpet backing, both main and secondary, packaging where porosity is required, industrial wipes, composites (marine sail laminates, table cover laminates, chopped strand mat), flooring, and backing/stabilizer for machine embroidery are all examples of products that use porosity.
- Automobiles and transportation. Gasoline, oil and air filtration, tarps, and transportation wrapping are all available.
- Acoustics. Sound attenuation, acoustic insulation for appliances, automobile components, and wall paneling
- Apparel. Interlinings, insulation and protective apparel, industrial workwear, chemical defense suits, shoe components, and backing/stabilizer for machine embroidery are all examples of products that fall into this category.
- Medical. Gloves, shoe covers, bath wipes, wound dressings, medication delivery, plasters, medical face masks, disposable clothes (foot coverings, coveralls), cleanroom wipes, pharmaceutical filters
- Packaging. Packaging for meat (absorbent pads), shopping bags, mailing envelopes, and shipping goods
- Furnishing. Pillows, cushions, mattress cores, and upholstery padding, as well as quilt batting for comforters
- Household. Filters, such as air, water, coffee, tea, and vacuum bags; meal prep wipes, housekeeping wipes, and surface cleaning
Why Non-woven Fabric Is So Popular Nowadays
Non-woven fabric, as we all know, is a very popular fabric due to its low cost, lightweight, and durability. It’s a fabric that doesn’t require spinning or weaving.
Textile staple fibers or filaments are aligned or randomly organized to produce a web structure, which is subsequently reinforced mechanically, thermally, or chemically. As a new environmentally beneficial material generation. Non-woven tote bags are commonly used. The non-woven fabric is light, with polypropylene resin as the major raw material for manufacture, with a proportion of only 0.9, making it only 3/5 cotton, fluffy, and non-toxic.
The non-woven fabric contains no chemical components, is very stable, non-toxic, has no distinct odor, and causes no skin discomfort.
The antibacterial property:
Polypropylene is blunt chemical substance, not insects, and can exist in isolation of liquid bacteria and insect erosion. The product is antibacterial, corrosion, erosion, and impact strength.
Good physical properties:
constructed of polypropylene spinning directly laid net thermal bonding, product strength is preferred above regular staple goods in no direction, strength, and transverse strength is comparable.
Because of the properties of non-woven fabrics, non-woven fabric bags are now utilized in various industries in our daily lives, such as garment packaging, food packaging, grocery packaging, and so on. Customers provide free exposure and endorsement by using attractive non-fabric bags.
So Why Non-Woven and Why Now?
Nonwovens are inventive, creative, versatile, adaptive, necessary, and biodegradable. Because this fabric is made directly from fibers, no yarn preparation activities are required.
The production procedure is quick and simple. Whereas it takes 6 months to produce 5,000 meters of woven fabric, it only takes 2 months to produce the same amount of non-woven fabric. Furthermore, the production costs are modest. Furthermore, nonwoven fabric has unique features such as increased strength, breathability, absorbency, durability, lightweight, flame retardancy, disability, and more.
Of course, we can’t overlook COVID-19’s global significance. In many nations, demand for non-woven fabric hygiene and medical products (such as surgical caps, surgical masks, PPE, medical apron, shoe covers, and so on) has surged 10-30 times.
Nonwovens have undoubtedly increased opportunities for everyday convenience. Nonwovens, like Henry Ford, made it possible to own a car and the Wright brothers made it possible to fly, have revolutionized various industries, appearing in hundreds of goods that would otherwise be too expensive or impractical to create profitably.
Conclusion
As a Non Woven geotextile suppliers to this evolving and essential industry, we are actively monitoring trends and collaborating with our non-woven customers. As they respond to changing markets and launch new products. When a new nonwoven fabric is introduced, the tape is frequently tested and reevaluated to ensure stickiness. When selecting the correct tape to splice, tab, and core to start a roll, the chemical makeup of the non-woven materials must be examined. With technological advancements occurring on a regular basis, resolving this issue will require a collective effort.
Please contact us if you are looking for your non-woven application or are experiencing difficulties with your unique splicing, tabbing, or core beginning job. We enjoy tackling tape problems!