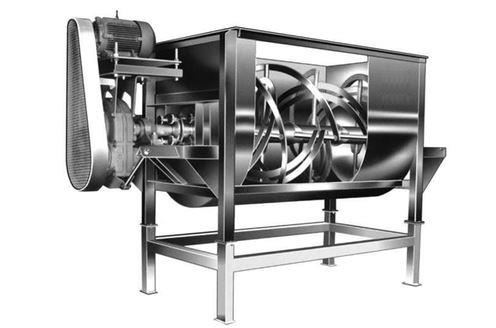
A ribbon mixer is an excellent piece of equipment in your facility. They can handle large batches with a quick turnaround time.
The first thing to consider when buying a ribbon blender is the materials it will be working with. The material density will help determine the blender size that would work best for you.
Materials of Construction
Ribbon mixers are powder blending machines that can handle various ingredients. These machines are multipurpose and can be used for mixing drugs, cosmetics, and chemicals and lubricating dry granules. They can also be used for coating solid particles with liquid additives or slurry mixes.
The interior of a ribbon mixer has a U-shaped chamber with an open top and bottom. The ribbon agitator moves in a countercurrent motion blending the materials inside the vessel. This results in a fast and effective mix with a shorter mixing time.
The materials used in the construction of these mixers are carefully chosen. For example, the used Stainless Steel undergoes multiple refining processes to ensure that it has the highest quality standards. They also meet GMP and FDA requirements. These are essential considerations for anyone that wants a durable and reliable machine. The motor is another vital part of the machine, and selecting one that matches the size and power requirement of the device is essential.
Design
Ribbon mixers blend dry powders and granules in the pharmaceutical, chemical, and minerals industries. They can mix various materials, from spices to instant recipes and drink mixes, pharmaceuticals, ceramics, polymers and plastic compounds, fertilizers, and more.
Moreover, ribbon mixer designs can be customized to match the needs of a specific application. For example, the explicit raw material may require the ribbons to be exposed to more shear force, increasing the number of stripes or the size of the agitators.
Other customizations include the type of agitator and the mixing duration. For example, paddle agitators are gentler on ingredients that are sensitive to shear, while double-bladed agitators can mix faster but will require more horsepower.
Choosing a suitable discharge valve is also crucial. An intelligent design can ensure that the mixer can discharge promptly without any wasted product. Options include:
- A full-length drop bottom.
- Standard pneumatic-end slide gate.
- Multiple sliding gates.
- A center-pneumatic discharge port.
Motor
Ribbon mixers are industrial machines that blend dry powders, granules, or other bulk materials. They can do this because they use a double-helix agitator that creates a back-and-forth folding motion. This mixing motion allows for the smooth, consistent mixing of different materials.
These machines also have a discharge valve at the bottom of their troughs, which makes it easy to release mixed material. They can be used for various applications, including pharmaceuticals, food production, animal feed, chemicals, paint, and more.
Many offer high-quality ribbon mixers that are made from quality and durable materials. Their equipment is certified to meet Good Manufacturing Practices and other international standards. Additionally, they offer a variety of sizes and designs to meet your specific needs. Their experts are always happy to help you select the best mixer for your particular application.
Weighing
Ribbon mixers excel at blending dry powdered materials. In the pharmaceutical industry, these versatile machines help produce tablets and other life-saving drugs by combining various formulations of chemicals into one smooth mixture.
A ribbon mixer works by agitating the material using a corkscrew-like metal blade. The outer ribbon of the machine moves the product towards the discharge, while the inner ribbon pushes the product away from the release. This movement ensures a complete mixing action and eliminates dead spots in the vessel.
Choosing the correct type of ribbon mixer requires knowing the size and density of your products. This will allow you to determine the working capacity of your batch and select a suitable model.
You can also choose to equip your mixer with an extrusion screw for thick pastes and other viscous applications. This will increase the agitation speed and improve the product’s consistency. Lastly, you need to consider the motor power requirements. You may need a heavier-duty motor or gear reducer if your application demands it.