Pneumatic systems
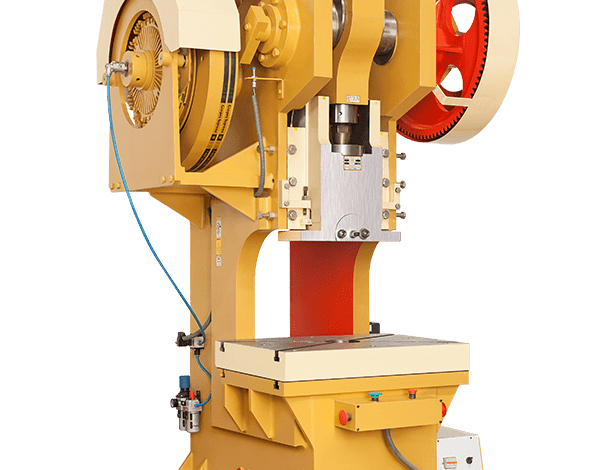
Advantages of the pneumatic systems
1) The pneumatic system provides cheaper and lighter equipment because they operate in air that is freely usable and does not require a solid construction.
2) No return line is required.
3) The pneumatic system is fireproof, explosion-proof and non-reactive, so it is a safer system. It can therefore be used in a fire hazardous area.
4) It is clean while the air is dry. It is therefore widely used in the food, electronics and automation industries
5) The pneumatic systems provides cheaper and lighter equipment when operating in air, which is freely usable and does not require a solid construction.
6) No return line is required.
7) The pneumatic system is fireproof, explosion-proof and non-reactive, so it is a safer system. It can therefore be used in a fire hazardous area. H Type Power Press
8) The pneumatic systems are clean while the air is dry. It is therefore widely used in the food, electronics and automation industries
Pneumatic system limitations.
1) High compression costs
2) Reduce accuracy
3) Working with noise
4) High operating costs
5) Low pressure application
6) Additional lubrication is required.
7) High compression costs
8) Decrease accuracy
9) Working with noise
10) High operating costs
11) Low pressure application
===
Pneumatic energy sources
Pneumatic energy refers to the force associated with air pressure. This pressure can be static or it can work. Most industrial machines use pneumatic energy and have at least one source of pneumatic energy. In order for most industrial equipment to function properly, it converts pneumatic energy into forms of kinetic and potential energy.
Pneumatic energy can be dangerous, so it is important that it contains content. The pneumatic energy must be checked for proper operation. According to the Office for Safety and Health at Work (OSHA), hundreds of injuries caused by pneumatic energy occur every year.
Eye injury is one of the occupational hazards of using pneumatic energy. These injuries usually occur by releasing pressure or blowing a puncture. Other common injuries are skin abrasions or sutures. This occurs when the skin is exposed to a high pressure fluid stream. Unexpected movement of the air pressure motor can also cause serious injuries to workers.
Risk of injury
Due to the risk of injury, it is very important to monitor pneumatic energy. Various sources are used to control pneumatic energy. One of these methods is pneumatic energy insulation. This resource uses various tools. Piston-type pneumatic valves adevices that separate energy. They do this by stopping the airflow and venting the system. Another source used to control pneumatic energy are interlocking devices. These tools work positively. In one example, they use a lock and key to keep the device in a safe position only.
===
The pneumatic system widely use throughout the industry and consumes more than billions of kWh of electricity annually worldwide. In order to improve the efficiency of the pneumatic system. An evaluation of its performance and measurement method must design and its application verify. In this paper, methods for evaluating. And measuring the performance of a pneumatic system presented for the first time. Second, based on the proposed methods, the power distribution of the pneumatic system investigate. Third, the analysis of the pneumatic efficiency of typical compressors and pneumatic components confirms the use of the proposed methods.
Methods of evaluation and measurement of the force
It can state that in the first place the proposed methods of evaluation and measurement of the force of the pneumatic system are effective. In addition, the efficiency of the pneumatic performance of the pneumatic air production system and the cleaning method is approximately 35% -75% and 85% -90%. In addition, the pneumatic force efficiencies of the pneumatic system of transmission and consumption methods are about 70% -85% and 10% -35%. And the overall efficiency of the pneumatic power of the pneumatic system is about 2% -20%, which is different from most suppression systems. This paper provides a method for analyzing and measuring the performance of a pneumatic system, thus laying the foundation for optimizing and saving the energy of a pneumatic system.
HOW TO MANUFACTURE HYDRA-PNEUMATIC CYLINDERS?
Pneumohydraulic Cylinder Unlike fixed pneumatic or rigid hydraulic cylinders, these hybrid cylinders rely on surface differentiation of the inner pneumatic piston rod assembly to increase the pressure of trapped oil on the working piston to provide a reinforced hydraulic cylinder. output. forces. Initially, both work on pneumatic, double-acting cylinders, stretching and retracting the workpiece with output forces typical of pneumatic cylinders. However, once the workpiece is in contact, the second pneumatically actuated cylindrical section pushes the rod into the oil section, closes it and increases the internal pressure.
Increased oil pressure
The increased oil pressure pushes against the working piston and produces more power, usually in hydraulic cylinders. Like other double-acting pneumatic cylinders, hydra-pneumatic cylinders use valves to control their movement. They have a four-way valve to control the approach and retraction movements and a four-way valve to control the oil pressure boost. This design combines the advantages of pneumatic and hydraulic cylinders without disadvantages. Compared to rigid pneumatic cylinders with a multi-stage design, these cylinders consume only about 1/4 to 1/3 of the air.
TYPICAL INDUSTRIAL APPLICATIONS OF HYDRA-PNEUMATIC CYLINDERS
Hydraulic cylinders designe for machine builders and OEMs for use in in-house presses and automation, as well as for the use of presses supplied. Presses are available with “C” frames as unaccompanied “H” frames, two- or four-column guide top supports, and table-mounted, pedestal, or machine-mounted configurations. Due to their modular design, machine builders can opt for a simple frame and drive design that facilitates integration into a larger assembly process, rather than a turnkey design that includes automation technology, controls, and so on.
Better process control: Our rollers allow separate control of the approach stroke and force stroke, allowing more complete process control without having to reconfigure the cylinder.
Higher retraction force:
Because our cylinders can generate more retraction forces, they can adjust the joints of heavier tools.
No energy savings:
Our cylinders do not use mechanical jumps to move the pistons, which can break and prevent / stop operations. There are no unexpected movements of the stored energy.
Better cost savings:
Our cylinders use less air than other pneumatic cylinders. Our cylinders take up less space. Generate less heat and noise. And cost less than buying a hydraulic cylinder and drive unit. In addition, they offer a much higher speed of operation and a lower risk of leakage. If the component under test has ports that differ from those describe by the height or size of the structure, connectors should use to connect to the correct pipes.
2. If the inlet and outlet ports of the component under test differ in structure or size, baffles and manometer connections appropriate to the ports shall use.
Application methods: Energy distribution in pneumatic systems
Due to the design of the pneumatic force, it is no longer difficult to calculate the efficiency of the pneumatic device and analyze the energy distribution of the pneumatic system. Furthermore, conventional pneumatic equipment and components such as compressor, filter, dryer, piping, cylinder, etc. can use. This feature represents the application of power distribution in a conventional pneumatic system. Meanwhile, methods for analyzing the energy losses. And efficiencies of typical pneumatic devices introduce. Read more about business, automotive, finance, app development.
Read more:Things You Should Know About a Segway Before Buying One