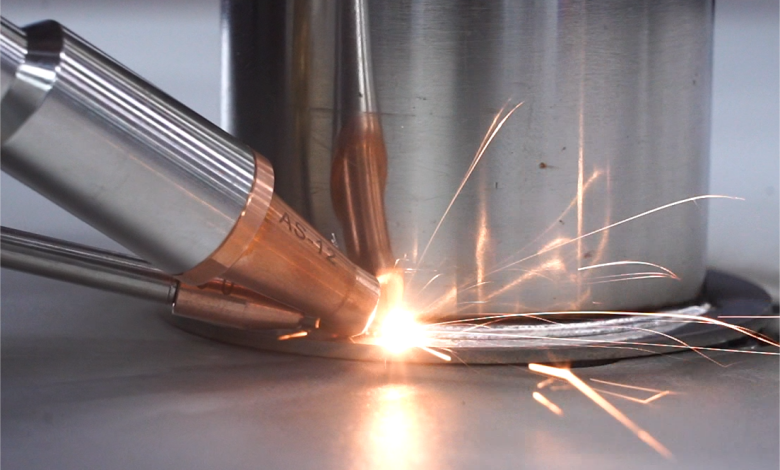
Introduction:
In the world of modern manufacturing and fabrication, laser welding has emerged as a highly efficient and precise method for joining materials. Whether you’re working with metals, plastics, or other materials, a laser welder can provide clean and strong welds. However, like any advanced tool, using a laser welder requires knowledge, skill, and proper techniques to achieve the desired results. Learn more about the world of laser welding and explore how to use a laser welder effectively.
Understanding the Basics of Laser Welding
Before diving into the practical aspects of using a laser welder, it’s essential to grasp the fundamentals of laser welding. Laser welding is a welding process that uses a high-intensity laser beam to fuse two or more materials together. The laser beam is focused on the joint between the materials, and the energy from the laser heats the materials until they melt and form a bond upon cooling.
There are two primary types of laser welding methods:
Conduction Welding
In this method, the laser beam heats the material’s surface, and the heat is conducted through the material to create the weld. It’s suitable for thin materials and applications where minimal heat input is desired.
Keyhole Welding
Keyhole welding is used for thicker materials. The laser beam creates a keyhole or hole in the material, and the material melts around this keyhole, creating a strong weld. This method provides deeper penetration and is suitable for thicker materials.
How To Use A Laser Welder?
1. Safety Precautions
Safety should be a top priority when using a laser welder, as it involves high-intensity light and potentially harmful fumes. Here are some essential safety precautions to follow:
Wear Appropriate Protective Gear
Always wear laser safety glasses that are suitable for the laser wavelength being used. Additionally, wear protective clothing, including gloves and a welding helmet.
Ensure Adequate Ventilation
Laser welding can produce fumes and gases that may be hazardous to health. Make sure you work in a well-ventilated area or use a fume extraction system.
Know the Laser Classification
Understand the classification of the laser you are working with. Class 4 lasers, for example, require extra caution and should be operated in a controlled environment.
Secure the Workpiece
Ensure the workpiece is securely clamped or fixed in place to prevent movement during welding.
Training and Certification
Only individuals trained in laser safety and welding techniques should operate a laser welder. Certification may be required in some industries.
2. Setting Up the Laser Welder
Setting up the laser welder correctly is crucial for achieving high-quality welds. Here are the steps to follow:
Choose the Right Laser Parameters
Select the appropriate laser power, pulse duration, and spot size based on the materials you are welding and the desired weld quality. Consult the equipment manual for guidance.
Focus the Laser Beam
Properly focus the laser beam on the joint area to ensure precise welding. Use a beam profiler or a camera system to assist in beam alignment.
Positioning and Alignment
Place the workpiece in the correct position and ensure that the laser beam is aligned with the weld joint.
Calibrate Sensors
If your laser welder has sensors for feedback control, calibrate them according to the manufacturer’s instructions.
Test Welds
Before starting the actual welding, perform test welds on sample pieces to fine-tune the settings and confirm the quality of the weld.
Laser Welding Techniques
Once the laser welder is set up, it’s time to focus on the welding techniques. The technique you use depends on the type of materials and the specific welding requirements. Here are some common laser welding techniques:
Continuous Wave (CW) Welding
In CW welding, the laser beam is continuously emitted and applied to the joint without interruption. It’s suitable for materials that require minimal heat input.
Pulsed Laser Welding
Pulsed welding involves the laser emitting short bursts of energy. This is useful for controlling heat input and minimizing distortion, making it suitable for thin materials.
Laser Hybrid Welding
Laser hybrid welding combines laser welding with another welding method, such as MIG or TIG welding. This can enhance weld quality and productivity.
Troubleshooting Common Issues
Even with proper setup and technique, issues can arise during laser welding. Here are some common problems and their solutions:
Porosity
If you notice small holes or bubbles in the weld, it may be due to gas entrapment. Ensure the workpiece is clean and free of contaminants, and adjust the shielding gas flow rate.
Cracking
Weld cracks can occur due to excessive heat input or improper joint design. Adjust the laser parameters to control heat input and ensure proper joint preparation.
Weld Distortion
Weld distortion can be managed by using proper fixturing, minimizing heat input, and controlling the welding speed.
Maintenance and Care
To ensure the longevity and reliability of your laser welder, regular maintenance and care are essential. Here are some maintenance tips:
Clean Optics
Keep the laser optics clean and free of dust or contaminants. Use appropriate cleaning solutions and follow the manufacturer’s recommendations.
Replace Consumables
Replace consumable parts, such as nozzles and lenses, as needed to maintain weld quality.
Monitor Laser Power
Use a power meter to monitor the laser output and make adjustments if necessary.
Conclusion:
Laser welding is a powerful and versatile welding method that offers precision, speed, and quality. By understanding the basics of laser welding, following safety precautions, and mastering the setup and techniques, you can harness the full potential of a laser welder in your manufacturing or fabrication processes. Remember that practice and experience play a significant role in becoming proficient in laser welding, so don’t hesitate to seek training and guidance to enhance your skills in this advanced welding technology.