Does Focus on Rates Makes Sense
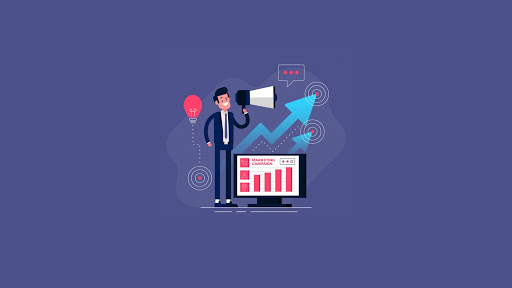
First of all we have to understand that cost management should not be viewed as a one-time initiative to be undertaken in reaction to adverse economic conditions. Oil and Gas companies must abandon traditional cost cutting responses to adverse conditions and should try to work collaboratively with suppliers to manage and control cost margins. Of course the concept of cost cutting works but it has its own limitations up to some extent. The focus of energy industry should be on utilizing the power of cross-functional teams with straightforward and clear short-term and long-term objectives. In this post, we will discuss some key factors which should be paid due importance other than cost reduction and delivery of cost efficiency.
Total Cost Visibility
This is a crucial and key element in direct materials sourcing and is recognized as the most apt method for improvement opportunities in strategic sourcing and supply chain process. Manufacturers agree that a clear understanding of total cost provides a competitive advantage. Such insight in cost visibility leads to higher margins, more successful new product introductions, and more stable supplier relationships. Best-in-class manufacturers leverage a deeper understanding of total cost to negotiate the optimal price for guaranteed capacity, lower supplier risk, and the right level of quality.
Utilizing the power of Cross-Functional Teams
One key success factor is how a continuous cost reduction approach is embedded in an organization. For sustainable cost reduction, this approach brings together cross-functional teams to review and implement opportunities along the entire lifecycle of a product/service and the entire value chain. Focused delivery of identified cost savings opportunities provides a platform for sustainable future growth. Individual workshops focus selectively on customer needs, value-added, product and service design, business processes, costs, quality, etc.
Focus on Baseline Production
With a key focus on oilfield management, getting more and more resources with less cost will improve your overall baseline production. Opportunities for increasing production from surface facilities can be identified by combining unplanned shortfalls with a criticality analysis. Real-time monitoring of critical assets to detect anomalies early and implement mitigation plans. Reducing mean time to repair critical assets by stocking more spare parts in the warehouse.
Focusing on Planning, Accountability & Service Quality
When we talk about Opex reduction techniques, remember that operational decisions should be made in reactive rather than proactive manner. A stronger focus on demand planning is required to prevent idle resources from incurring costs and better anticipate workload and resource requirements. A culture of accountability and clear cost ownership should be reinforced. Conducting periodic project-assurance reviews and setting up phased milestones for investment decisions will help ensure that capital is only committed to activities with justifiable business cases. Companies should aim to establish lean organizational structures that clearly delineate responsibilities and enhance the free flow of timely and accurate information along the chain of command.
Getting a sustainable approach with a focus on above mentioned aspects will allow companies to view their perspective in a broader sense with cost as just one of the major factors, and those which are bold enough to change will thrive in industry.