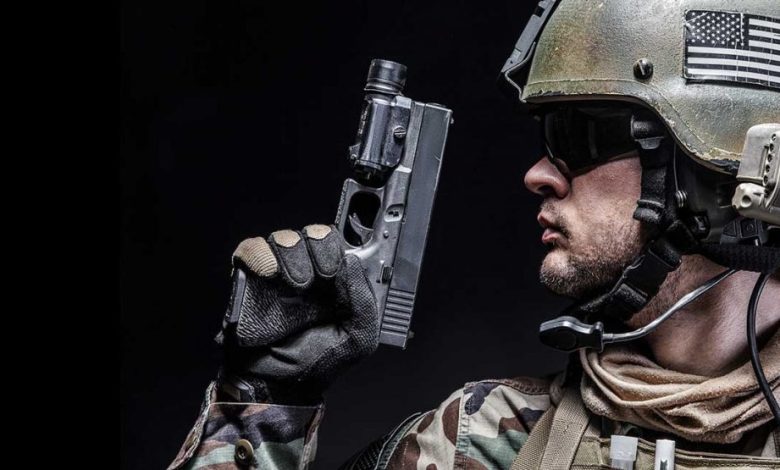
The process of Parkerizing is an old one. It was first patented in 1926 by H.S. Parker, the founder of the Parker Company. The process involves immersing metal parts into a chemical bath that contains phosphoric acid and then heating it, thus creating a black protective finish that protects the parts from corrosion. However, it wasn’t until World War II that the Parkerizing process was used extensively in firearms manufacturing, when it was used on guns like the M1 Garand and the .50 cal Browning Machine Gun for increased corrosion resistance.
Todays modern version of this process makes use of phosphoric acid combined with other chemicals, such as rust inhibitors, thiocyanates and fluorides. One of the main ingredients in modern Parkerizing is zinc phosphate, which reacts with the phosphoric acid to form a protective phosphate coating on the pieces being processed.
The process itself involves submerging gun parts in a tank of a chemical solution for varying lengths of time, depending on the material of the part and its desired finish. The chemical solution is heated to anywhere from 60 to 100 ̊C (140-212 ̊F), with an optimum temperature of around 80 ̊C (176 ̊F).
The chemicals used in this process are very hazardous, even in small quantities, so they are shipped in steel drums to prevent their contents from evaporating. The chemical bath is heated at the point of use; those who work around this process must wear protective gear such as gloves and eye goggles.
After it has been submerged long enough, the part will then be removed and hung up for draining and oiling. After this, it is put into a tank of gun oil and heated to approximately 100 ̊C (212 ̊F) until the oil has evaporated off. The part must then be allowed to cool before being handled.
The Parkerizing process will create a black protective coating on the surface of the parts undergoing the process. This protective coating is effective enough to prevent corrosion when exposed to moisture and humidity, but not so much that it cannot be removed fairly easily when necessary.
The black color that Parkerizing provides can be dyed using certain chemicals in order to achieve other colors such as green or blue (Smithsonian). This type of coloring does decrease the effectiveness of the Parkerizing process, since it is an interstitial corrosion inhibitor, but can still provide some protection against corrosion.
There are other ways to dye Parkerized parts this includes using dyes soaked into cloth or paper that are then attached to the part with adhesive tape. The best way to do this though would be by spraying the dyes onto the part.
One of the big downsides to Parkerizing that has made it less popular in recent years is that this process does not adhere well to aluminum.
Aluminum alloys are becoming more and more common in gun parts, specifically receivers, due to their strength relative to their weight ratio. Since Parkerizing only protects parts from corrosion, treatment against wear is still needed for aluminum gun parts.
We hope this helps you better understand the Parkerizing process and the benefits it has on metal surfaces.