Investment Casting
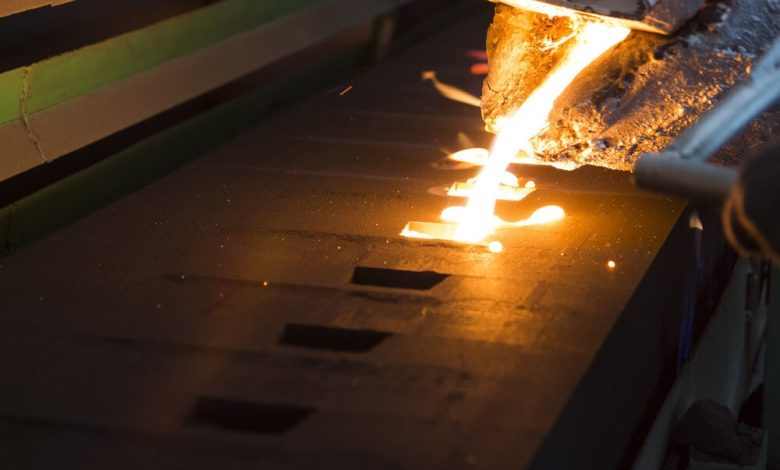
Investment casting is the possibility of manufacturing complex parts and components. The process of designing and manufacturing the required workpieces involves several specific steps. ItĀ so call because the workpieces make around an encapsulated casting which is later removed when the workpieces pour into the mold. And placed. pressure die casting manufacturers India
Step 1:
Create a die/pattern The first step in the process is to make a die or pattern of the desired workpiece. The pattern make of wax. It can be injection molded in one piece, handcrafted from a block of wax, or 3D printed with the appropriate wax material.
Step 2:
Attach the wax patterns A fusion casting tool involves creating multiple wax patterns and attaching them to a “gate” device. This tool is used to cast metal or other materials to eventually create the desired workpieces.
Step 3:
Assembling the wood The wooden assembly ends with the assembly of the wax patterns on the “gate” device. This step called a tree because each individual wax pattern is a “branch” and once the process complete it becomes the finished work piece. You may have wooden builds in new board games that require pieces to be removed for use.
Step 4:
Create the shell Once the wood is assembled, the next step is to add the shell molding around it. First, the wood is immersed in a ceramic slurry. It is then immersed in a stucco of fine sand. The cast must be completely dry before use. These two processes may completed several times until the mold is thick enough to handle the stresses of casting.
Step 5:
Removing the wax Before the desired material goes into the new shell mold, the wax patterns must first be removed. This is usually done by heating the wax in an oven. Steam can also used to heat the wax. The mold is placed upside down to allow the liquid wax to flow out. And reused to create new wax patterns.
An alternative procedure for wax removal is to heat the wax so that it is “burned off” and completely removed from the shell formation.
Step 6:
Pour the mold After the wax is removed, there are openings in the shell that are cast in the form of formal wax patterns. Molten metal or other liquid material is poured into the casting. The mass remains in the form until it cools completely. And solidifies.
Step 7:
Remove the shell cast A hammer or other tool used to remove the shell molding until only the original wood remains. Instead of wax patterns, finished workpieces are attached to the wood. After removing the casting, the workpieces are carefully cut into the wood.
Step 8:
Shutdown Each workpiece is checked for imperfections. If any are found, they are removed and the material is recycled. The final step in the fusion casting process is the application of various finishing methods to the workpieces. They can be sanded, painted, smoothed, machined, etc.
To achieve the desired result. A metal part make by the lost wax process The casting tool is suitable for large quantities or complicated workpieces that require precise details. The exact process steps can. And will vary depending on the complexity of the workpieces being produced. To learn more about investment casting and whether it is the best solution for producing the workpieces you need
Why choose investment casting services?
Having the right equipment for the investment casting process is essential. At The Federal Group USA, we use state-of-the-art technology to ensure the success of every project. Below is just some of the investment casting equipment that we leverage:
Shell-making equipment
Specialized shell-making equipment Highly automated robotic molding machines Horizontal vacuum precision furnace Vertical vacuum precision furnace High-pressure gas quenching vacuum furnace Short runs or high-volume production Reliable quality assurance equipment Automation We use the latest wax processing technology. Our semi-automatic wax injection machines allow us to make wax patterns quickly and reduce the time it takes to finish the project.
Our dewaxing machines quickly melt the pattern without cracking the ceramic shell. We use specialized equipment to pour the molten metal without creating air pockets, minimizing the risk of defects. A thorough quality assurance process follows.
Materials investment casting steel Pictured above: Raw billets / ingots used for investment casting. We can work with the following materials and more: Carbon steel and most steel alloys, brass, bronze, copper, aluminum, and Stainless Steels including Duplex 2205, 2507, and others.
Yield strengths
super duplex stainless steel with 25% chromium, 4% molybdenum, and 7% nickel alloy. They designe for applications that require exceptional strength and corrosion resistance. Duplex 2205 A two-phase, ferritic, austenitic 22% chromium, 3% molybdenum, 5 to 6% nickel alloy. Duplex 2205 is the most widely used duplex stainless steel grade and characterized by high yield strengths. It has good fatigue strength and demonstrates outstanding resistance to stress corrosion cracking, crevice, pitting, erosion, and general corrosion in severe environments.
300 series Superior corrosion resistance Non-magnetic Scratch-resistant 400 series Magnetic Greater strength than carbon steel. Suitable where thinner materials/reduced weight needed Grey, Ductile, and White Iron Tool steels, mild steel, alloy steels, etc. It used for various purposes for ease of machinability. Ductility or compressive strength Aluminium Investing in aluminum castings makes it possible to produce parts with complex shapes more quickly.
The process is also more flexible when using different types of compounds. Parts produced by this process have tighter dimensional tolerances and a better surface finish. This method requires less processing and processing. Copper / Bronze Excellent machinability Corrosion resistance Aesthetics Copper-based alloys Corrosion resistance Good luck Conductivity.
Fluctuate in the market
Thermal and electrical The price of copper can fluctuate in the market. Therefore. It is important to reduce the amount of waste in the production of complex copper components. Investments are a great way to reduce this waste. Magnesium Excellent dimensional stability Good construction material Ability to create fine details
Traditional metal casting techniques include lost wax casting, plaster mold casting, die casting, and sand casting to name a few. These metal casting processes can complete in a foundry or jewelry studio.
Metal casting processes have been known for thousands of years. And widely used to make sculptures, jewelry, transportation, weapons, and tools.
Casting often used to create complex shapes that difficult. Or uneconomical to create by other methods. Heavy equipment such as engine beds, propellers, etc. It can easily shaped to the required size instead of having many small pieces together.
What is the casting process like?
Casting processes involve the use of molten material, usually metal. This molten material then pour into a mold cavity that takes the shape of the finished part. The molten material then cooled. Where the heat usually removed through the mold until it fixed in the desired shape.
Metal casting has two main categories: reusable mold processes and reusable mold processes. In both processes, the caster pours metal material into a crucible, pours it into a mold. And after the metal cools and solidifies, removes the material from the mold or casting.
The basic process of metal casting involves creating a pattern and mold, then pouring molten metal into the mold. You take a solid metal casting and complete your piece. This process adapted for different types of metal casting, with shapes, sizes, etc. Read more about business, automotive.
Read More: Casting and other Machining methods