Press brake
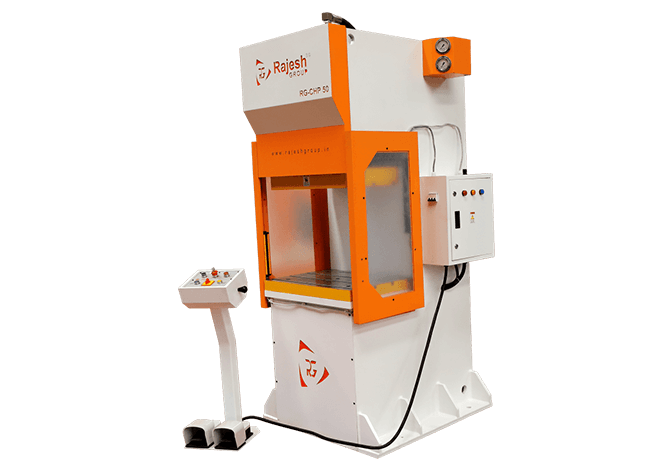
Pressure brakes are a must in almost every metalworking shop. Unfortunately, even though they are one of the most important and sought-after machines in the store, they still don’t understand them – not even professionals. To help you better understand edge presses, we have compiled this short guide for laymen. C-frame hydraulic presses
What are press brakes?
Pressure brakes are machines that form sheet metal lengths. These boards are often used in manufacturing, in industrial applications and also as parts for other equipment. Most brake pads are characterized by the ability to compress metal and the total length of the bend; is expressed in numbers (eg total PPI or pressure in pounds per inch). It comes in many forms and has always designed tools and accessories to create multiple custom components. Press brakes fall into two main categories: mechanical and hydraulic. In the following sections, we discuss the differences and explain the distinctive features of each style.
Mechanical press brakes
The mechanical brake pedal is controlled by the motor in the device. This engine rotates a large flywheel at high speed. The engine operator controls the flywheel via a clutch that adjusts the remaining moving parts to fill the metal. The mechanical brake pad is more straightforward, especially in terms of electronics, which speeds up maintenance and operation. They can handle tons two to three times their natural value, given the nature of the mechanisms. The main disadvantage of using a mechanical brake pedal is that the ram inside the engine must complete the entire cycle when it is engaged and irreversible. This creates some safety concerns because the operator makes a mistake and sets certain machine limits. One of the possible dangers is the possibility that the brake pad will lock if the ram goes too far.
Hydraulic press brakes
Hydraulic press brakes exert hydraulic pressure to push the ram, instead of relying only on mechanics. It can have more than one cylinder and gives the operator more precise control in corners. The result is a very precise and custom rotation. Like mechanical press brakes, hydraulic press brakes have some specific disadvantages. In principle, they cannot exceed their marked tonnage. If your project requires flexibility, mechanical brake pads may be preferred.
Press the brake controls
The first generation of press brakes had only one axis of movement for turning. They are more limited compared to modern machines with 12 or more programmed axes of motion. Modern brake pads are very accurate and provide a graphical representation of the end result to help the operator. Newer computers also shorten setup times. They can easily calculate the optimal settings based on the materials used, their dimensions, and the desired results. These calculations are performed manually during the day. Types of bending.
Pressed brakes
There are two ways in which pressed brakes can bend metal. The first is called bending because the ram pushes the metal into the bottom of the die. Low bends will result in very precise bends and less reliance on the press brake itself. The downside is any tool because they are made for a specific bend, so you need to buy a new one for each angle you want to make. Bending in the air leaves an air tube between the ram and the bottom of the die. This allows the operator to meet all the return springs provided by the material. These types of dies should only be replaced if the material thickness is too large. The disadvantage of air bends is that the accuracy of the angle is affected by the thickness of the material, so the sheep must adapt to it.
There is no denying that brake pads are one of the most useful tools a metalworker can make. Does your practice require a very good brake pedal? Quantum Machinery Group has everything your business needs to succeed.
Industries
Industries around the world are growing at an incredible rate due to technological advances. Various machines and tools can now be found that will help the industry significantly. The manufacturing sector also has its own range of tools and machines that have helped it flourish over the centuries.
The CNC Press Brake is one such tool without which the manufacturing industry and manufacturers would not be able to make progress. In this article, we will learn all about the CNC press, how it works, and its other functions. If you are in this business, it will be very beneficial for you to understand CNC press brake machines working, so if you are ready, let us get started!
About CNC press brake machine
Let us first understand what a CNC press brake machine is before getting into its working mechanisms. A CNC press brake machine is a tool that has CNC or Computer Numerically Controlled system integration in it. With the help of the CNC system, the machine is able to efficiently bend and manipulate metal sheets, be it be over a few millimeters or a few meters long.
The structure of a CNC press brake machine can be of two types. They are as follows:
Type 1 (Down Forming): Consists of a fixed bed (bottom) that has a v-shaped tool attached to it. There is an end beam (also V-shaped) that receives the force. And presses the metal against the V-shaped tool.
Type 2 (Up Forming): This type of CNC press brake has the same properties as type 1. However, with this type, the upper part is fixed, while the lower part is a movable counterpart.
Regardless of the type, the results are the same, without limiting the form and design of the result. Now that we understand what a CNC press brake is, we will now come to understand how it works. Work on CNC press brake
The CNC press brake is a mechanical device driven by a hydraulic or electrical system with an attached AI program for precise and precise bending of the raw material.
Information about the product
The way it works is easy to understand. You must first enter the information about the product you want to create on the CNC press. This information should be accurate, with right angles, etc. Once the computer analyzes and understands the instructions, it starts operating the machine. The machine works on hydraulic or electric energy. Depending on the type of your machine (type 1 or type 2), the force will act on the individual moving parts of the machine. This allows the moving parts to hold the metal blade against the fixed part and thus create the desired bend.
Sheet metal
For CNC machines, the machine will transfer the sheet metal according to the instructions provided by the computer. The result is – you get the product you want, with precise curves and accuracy. You can change the V-shaped tool, usually called the die (attached to the fixed part) and the knife (attached to the moving part), to the shape you want to create. There are many tools on the market for this purpose.
Various parts of CNC press brake
The CNC press brake has many functions and features that you can use in many ways. Below the basic parts supplied by Accurl together with their CNC braking machines.
Purchase guide for CNC press belt machine
The CNC press brake is a long-term investment for your business. So you want to make sure you invest in the right machine. Here are some things to keep in mind when looking for the perfect CNC press:
You must take into account the materials you will bend into the machine. Keep in mind the type and thickness of the materials.
Think about the complexity of the designs and curves that you will make. If your designs are complex, you should consider buying an extra-axle machine to make your curves perfect.
Think about the amount of materials you make. If you are considering series production, CNC brake machines are the ideal option. You need to consider the size of the machine as well as the workplace. If you buy a very large machine but do not have enough space to operate it. Everything is lost.
Think about the accuracy of the bends you make. Different machines offer different accuracy. You may also want to consider purchasing a toolkit to improve accuracy and end results.
Read more: 10 Ways Online Roulette Games Can Improve Your Business